What is the Unified Construction Method®?
The Unified Construction Method® is a patent applied building method for tiny house vehicles (tiny houses on wheels/trailers) developed by Fred Schultz of Fred’s Tiny Houses Pty Ltd. Fred developed the Unified Construction Method® to make his house vehicles safe to transport, suited to the Australian climate and comfortable to live in all year round .
Suitable for timber framing and steel framing methods.
There are 4 Elements to the UCM®
Element 1: Floor Joist Tie Downs.

The safest way to attach a tiny house to the trailer is by using a horizontal bolting system. Most THV’s are fastened using some sort of a vertical fastening method which makes if vulnerable to the upward lifting force that comes from moving fast down the road. Any horizontal fastening method will be superior to vertical fastening method. The Unified Construction Method® Element 1 accomplishes this horizontal fastening by bolting floor joist through our steel floor joist tie downs welded to the trailer.
The floor joist tie downs integrate the trailer with the floor to create the first element of a unified whole. It is strong, integrated and allows for a truly insulated floor.
Element 2: Stud Wall Tie Downs.

Eight steel stud wall tie downs extend up from the trailer through the bottom plate to the stud walls of your tiny house vehicle (THV). Element 2 of the Unified Construction Method® (UCM®) creates a strong and secure connection between trailer and the walls of your THV, while once again using the superior advantages of a horizontal bolting system. Element 2, stud wall tie downs function independent of Element 1, the floor joist tie downs so both work together, but do not rely upon one another to give strength and unity to your THV.
Element 3: Bracing Plywood Sheathing.

The Unified Construction Method® Element 3 goes beyond traditional bracing plywood used in timber frame residential construction, even in cyclonic areas. This method secures plywood sheathing from floor to roof with vibration-resistant adhesive and other fastenings. Tiny House Vehicles (THVs) require higher standards than the Building Code of Australia, which is designed for stationary homes, not for structures that travel at high speeds and endure constant vibrations. By wrapping the entire house from trailer to roof in this unified manner, the Unified Construction Method® creates a strong, lightweight, and vibration-resistant connection. While the tiny house movement is still largely unregulated, this method is the best unofficial standard available for THVs.
Element 4: Radiant Barrier.

A radiant barrier, installed in the ceiling, blocks 97% of the sun’s radiant heat, essential for tiny house vehicles (THVs) in Australia. Summers are extremely hot, and solar panels mean your THV will be in direct sunlight year-round. Unlike conventional houses, THVs lack an attic, so heat from the roof travels directly into the loft, where you sleep near the hottest part of the house. More bulk insulation won’t stop this heat transfer, but a radiant barrier will. The Unified Construction Method® uses a standard product in an unconventional way to keep your interior ceiling at room temperature, making it feel like you’re parked under a tree instead of the blazing sun.
Get the Unified Construction Method® with your Fred's Tiny House Trailer
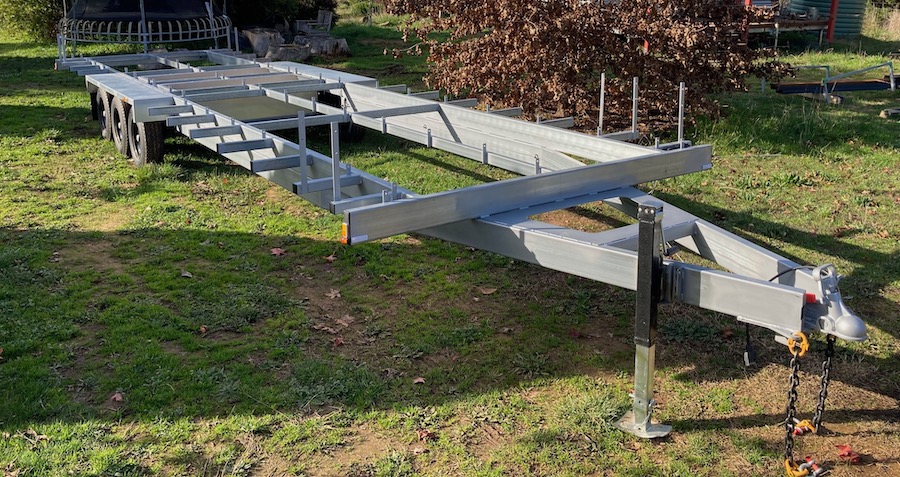
A safety standard for tiny house vehicles.
A tiny houses on wheels is both a vehicle and a building.
Tiny houses that are built on trailers are vehicles. Even though they are not motorised, they are vehicles, which means they need to be built to withstand the physical forces that they encounter during transportation.
Many tiny house builders design and build their tiny house vehicles the same way that they build houses on solid foundations. They have not thought about the significant road vibrations or wind-forces that the house will be subjected to or how to keep the whole structure together in the face of these forces.
The Unified Construction Method® is the only tiny house vehicle building method that considers these forces. The Unified Construction Method® considers every connection point in the construction of the house and it uses building materials and fastenings to create a solid, unified whole that is vibration resilient and super strong and will last the long life of the tiny house vehicle.
Safety
Tiny house vehicles are subjected to incredible forces during transport that conventional houses are not.
Wind-force: On the road, tiny house vehicles may have to withstand hurricane winds above 90km per hour, known as ‘storm-force’ winds that the Australian Bureau of Meteorology states is ‘seldom experienced inland’ and from which we can expect ‘trees uprooted; considerable structural damage’. This is because conventional houses built on foundations are not built to withstand this kind of wind force. So conventional building standards cannot be relied upon to build safe tiny house vehicles.
Vibration: Tiny house vehicles also have to withstand long-lasting vibrations that stress every connection point in the whole structure. Think of the road vibration as being like that in an earthquake. But earthquakes only last for about a minute. Tiny house vehicles have to withstand earthquake conditions for hours and hours across their lifetime.
The Unified Construction Method® was developed to create the strongest possible tiny house vehicle, protecting it against the significant transportation forces and making the structure lightweight and liveable year-round. It is also a method that is build-able by DIY builders as well as professionals and uses readily available building materials in unconventional ways.
Consequences of using inadequate building methods
There are several layers of consequences for using inadequate building methods when building tiny house vehicles.
For the tiny house owner: You don’t want your tiny house to break or endure any damage during transportation. It would be such a shame to see all the hard work, time and money you put into your beloved tiny house to be ruined or damaged during transport. Just imagine the cracked facades or leaks because of road vibration that your tiny house couldn’t withstand. You don’t want the disappointment, expense or embarrassment of having a tiny house vehicle that’s not built for purpose.
For fellow travellers on the road: No-one wants to cause a road accident. Unfortunately, if inadequate building methods are used to build tiny house vehicles, parts of the tiny house may break or come loose during transport and cause major road accidents.
For the whole tiny house movement: A road accident involving a tiny house vehicle will be cause for a lot of negative attention in the media. Worse yet would be a road accident caused by a problem with a tiny house vehicle. That kind of front-page news would spur regulators to crack down on the tiny house movement and implement any number of rules or regulations that could threaten the tiny house movement from growing or from tiny houses being a viable option for most people.
Everyone who builds a tiny house vehicle carries the responsibility of the tiny house movement on their shoulders. When you build a strong, vibration resilient tiny house vehicle, you are acting responsibly on behalf of yourself, others around you and the whole tiny house community.
Current lack of building regulation for tiny house vehicles.
At the moment there are a few regulations that determine the parameters of tiny house vehicle construction. They are:
- VSB1 = Roadworthy guidelines for all vehicles in Australia. ie: Where the door has to be placed on a caravan.
- The VSB1 is underpinned by the Australian Design Rules = Set out Australian Standards for everything. ie: Minimum standards for vehicle lights to make sure it is safe on the roads.
There are NO building regulations for tiny house vehicles that cover the construction methods used.
The closest thing to a building regulation that could be applied to a tiny house vehicle is the Building Code of Australia (BCA). The BCA defines the minimum standards of building techniques to be used on buildings (think conventional buildings on foundations). But, as we said before, tiny houses are not buildings. They are vehicles.
Since the BCA outlines standards that are designed for buildings, not for vehicles, it is not safe to rely on the BCA for building a safe tiny house vehicle.
“But I’m only going to move my tiny house once or twice…”
If you lived in an earthquake zone, you would build your house to be earthquake proof. You wouldn’t build it for completely stable conditions and think: ‘I will only experience one or two earthquakes… I’ll get away with this design.”
Well, travelling down the road is equivalent to an earthquake for a tiny house vehicle. So it needs to be built to withstand earthquake conditions. Even if you didn’t plan on moving it ever.
This is because if a tiny house is built on wheels someone will want to move it. Whether the tiny is in your possession or after it changes hands, it is valuable when it is in the right location. And there’s no way of knowing when a poor design will come apart. So it doesn’t matter if you only move it once or never at all. If it is built on wheels, chances are someone will try to move it, and that needs to be safe as… houses.
Get the Unified Construction Method® when you order your Fred’s Tiny Houses trailer.